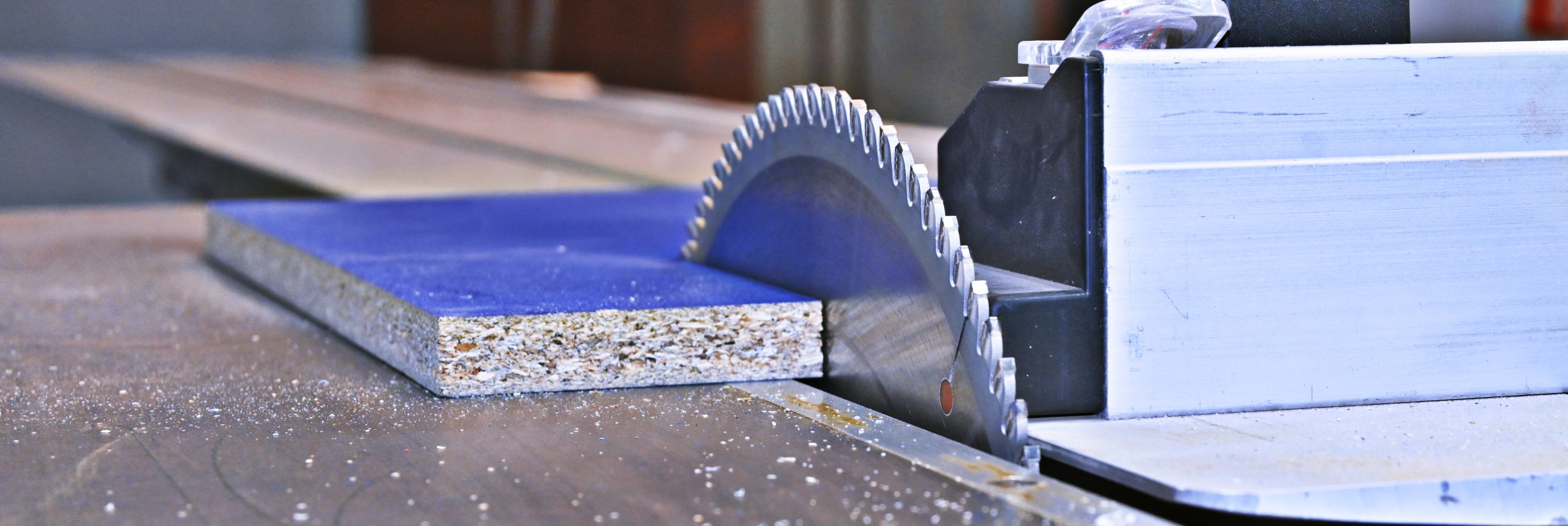
YOUR DESIRED MACHINES
CATEGORY
MODULAR FURNITURE MACHINERY
SOLID WOOD MACHINERY
- Thickness Planner
- Double Side Planner
- Surface Planner
- Combined Machine
- Planning Saw Machine
- Four Side Moulder
- Finger Joint Machine
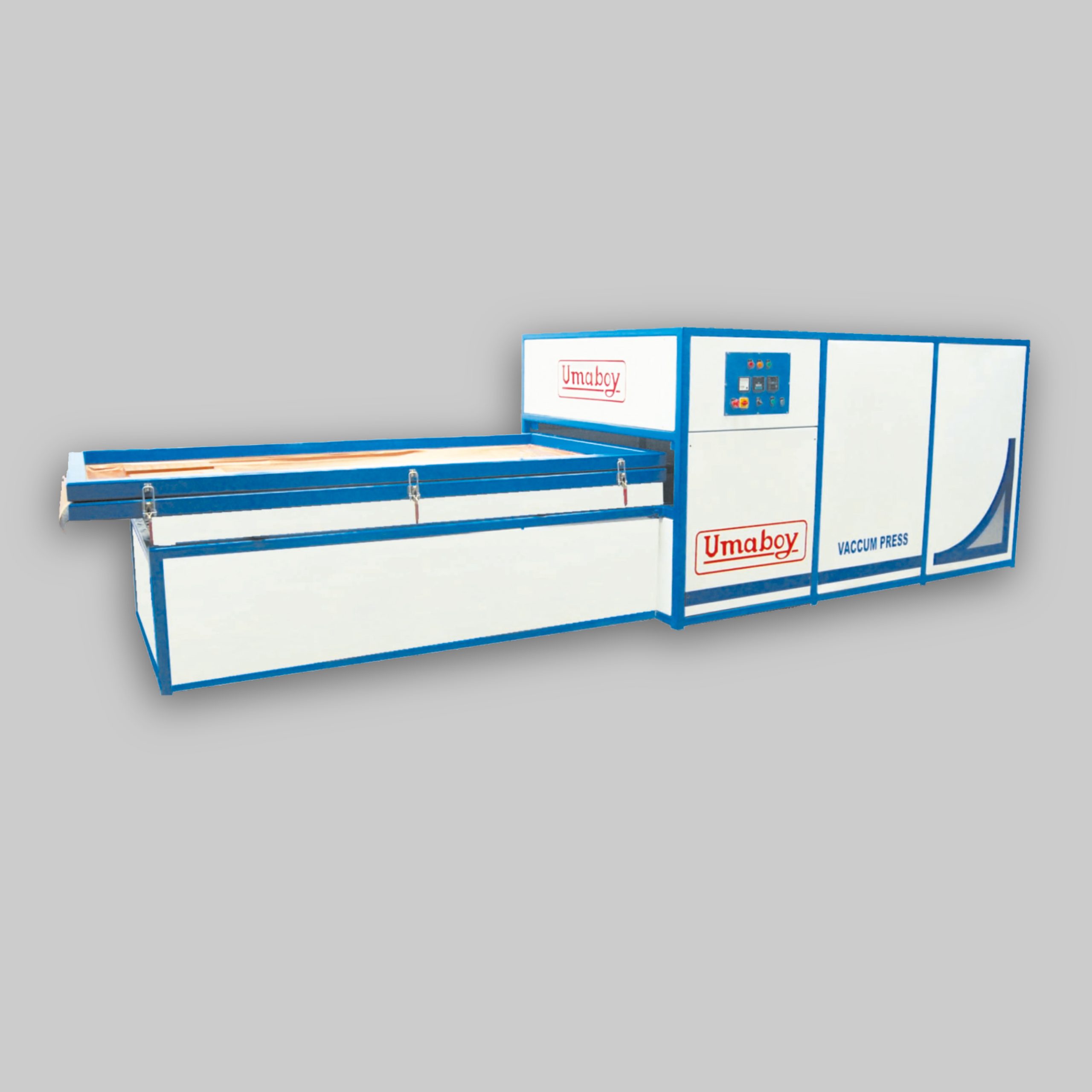
VACUUM PRESS MACHINE 1010
to create low pressure, which ensures even application of pressure across the entire workpiece.
Have Any Question ?
WE ARE HAPPY TO HELP
About Vacuum Press Machine
Buy Vacuum Press Machine for top-notch performance and reliability in your industrial operations. A Vacuum Press Machine is a woodworking tool used to apply a consistent and even pressure across a surface by using a vacuum. It is commonly used in laminating, veneering, and molding operations to ensure a tight bond between materials and to achieve a smooth, wrinkle-free finish. We are Leading manufacturer of Vacuum Press Machine UVP 1010, delivering advanced solutions for precision and efficiency in industrial applications.
Application of Vacuum Press Machine
Features
- Vacuum System: Utilizes a vacuum pump to create low pressure, which ensures even application of pressure across the entire workpiece.
- Flexible Membrane: Adapts to various shapes and surfaces, providing uniform pressure and eliminating wrinkles or bubbles.
- Heat Capability: Some models include integrated heating elements for enhanced bonding and curing, especially with adhesives.
- Control Panel: Allows for precise adjustment of vacuum pressure, temperature (if applicable), and timing.
- Large Work Surface: Accommodates a variety of workpiece sizes and shapes, making it versatile for different applications.
Advancements:
- Digital Controls: Modern machines feature advanced digital interfaces for more accurate and user-friendly control of vacuum pressure, temperature, and timing.
- Improved Vacuum Technology: Enhanced pumps and seals provide more reliable and efficient vacuum performance.
- Automatic Features: Automated systems for vacuum application and pressure release streamline operations and improve consistency.
- Enhanced Heating Systems: Better integration of heating elements for faster and more uniform curing of adhesives and materials.
- Advanced Materials: Use of more durable and flexible materials for membranes and components, improving the machine’s longevity and adaptability to various workpieces.